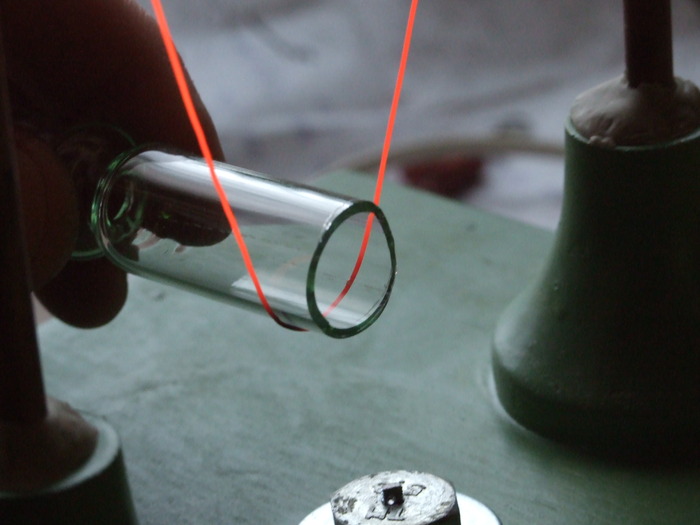
Фото 1. Электрорезка в работе.
В стеклодувном деле, разновидности, занимающейся размягчением стекла в пламени горелки, имеют дело преимущественно с заготовками - трубами и твердыми палками (огрызками, стрелами). Используя заготовки разного диаметра, придавая им разнообразную форму и спаивая полученные элементы между собой, мастер-стеклодув получает весьма сложные инструменты. Поэтому вся подобная работа со стеклом состоит из небольшого набора относительно простых операций и приемов.
Самыми простыми операциями, еще до горелки, являются заготовительные операции – разрезание заготовок-труб на куски нужной длины. Существует несколько способов такой резки, наиболее практичным для небольших труб является использование стеклодувного ножа. Поставили метку в нужном месте – царапина и труба рвётся. Торцы заготовок обычно получаются удивительно гладкими. Метод очень хороший – быстрый, точный, качественный, но для подготовки приходится прикладывать немало усилий, что не всегда и не везде возможно.
Распространенная задача — отрезать короткие хвостики возле стеклянного элемента или края трубки. При попытке разбить стекло в таких местах вероятность травм и порезов «оператора» очень высока».
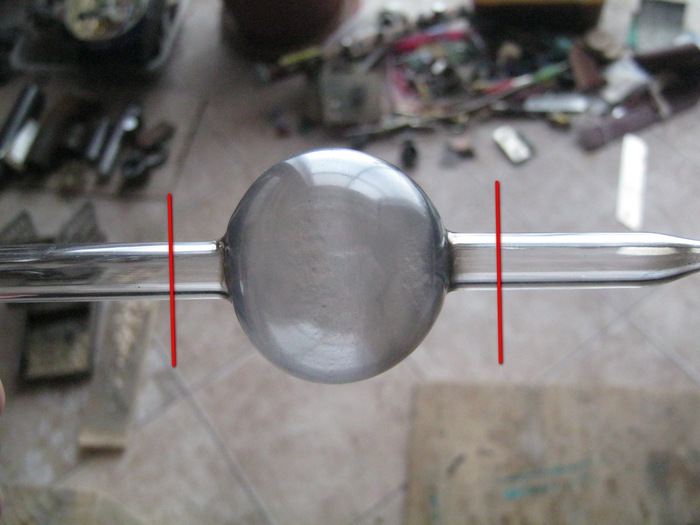
Фото 2. Тренажерный элемент представляет собой шарик из свинцового стекла с тонкими стенками. Попытка отрезать его обычным методом соскабливания, скорее всего, испортит его, и вы одновременно порежете пальцы.
В таких случаях эксплуатируется обычно крайне неприятное свойство стекла – разрушение вследствие термического удара. В нужном месте также делают небольшую царапину стеклодувным ножом, как бы указывая путь и сильно нагревая, или, наоборот, быстро охлаждая нагретое. Известный способ резки бутылок, например, заключается в обматывании нагретой электрическим током заготовки проволокой. Более практичным и универсальным является специальный стационарный агрегат с V-образным элементом горячей обработки, натянутым на стойках (рис. 3).
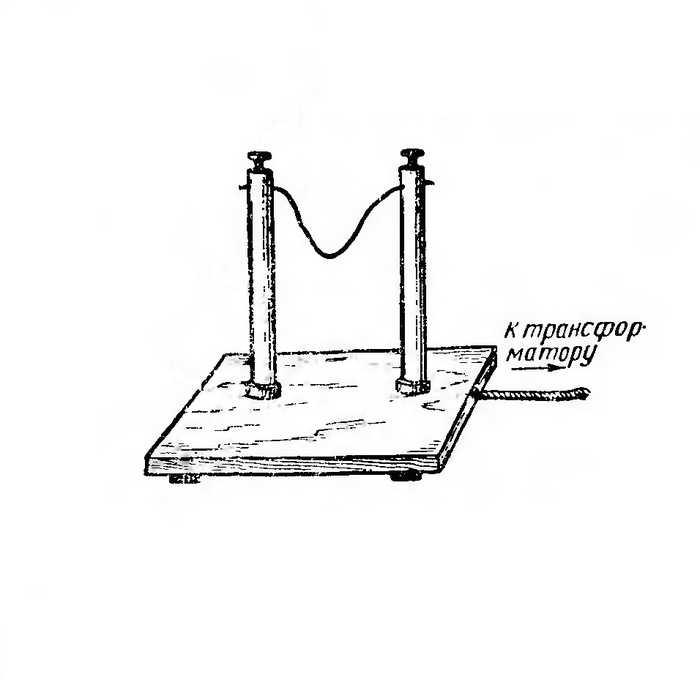
Рис. 3. Резка стеклянных трубок. Рисунок из книги «Стеклодувка» Легошин А.Я., Мануйлова Л.А.
Покопавшись в закромах, я нашел подходящий трансформатор и немного нихромовой проволоки Ø 0,5 мм. Трансформатор достаточной мощности, широкий и плоский, можно встроить в подставку или, точнее, держатели разместить на крышке коробки. Кроме того, у него уже было несколько готовых сильноточных обмоток, одна из которых согласилась работать с куском моего нихрена разумной длины. Также имелось практичное крепление крышки с крупной резьбой по оси.
К точке.
Основа ящика была сделана из фанеры. Для толстых стен я подобрал остатки деревянного ящика от своего старого агрегата. Я вырезал из них более качественные детали на торцовочной пиле.
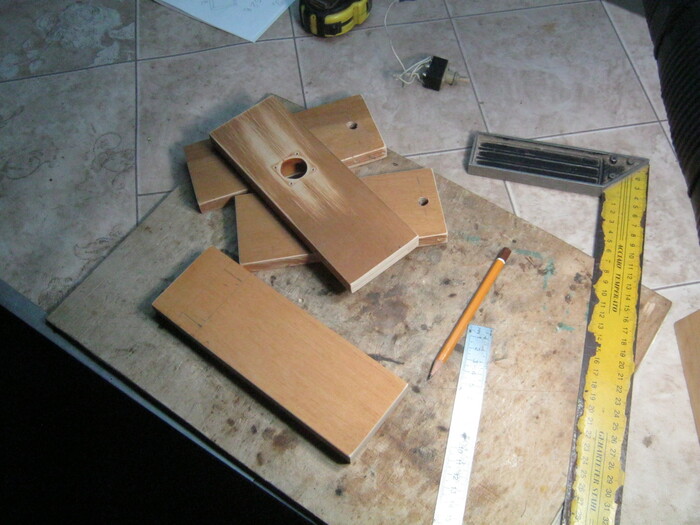
Фото 4. Стенки трансформаторного ящика. Несколько дополнительных отверстий не сильно портят внешний вид. На передней панели имеется маркировка светодиода – индикатора включения устройства и выключателя питания. Я определенно хотел кулисный переключатель. Да, вот он — вверху фотографии.
На стенках корпуса расположены два установочных устройства – сетевой выключатель с индикатором на передней панели; блок предохранителей сзади. Конструкция этих мест проста и утилитарна — устройства устанавливаются на небольшую дополнительную панель из тонкого текстолита и крепятся к передней части фанерного корпуса, перекрывая и закрывая специальную дорожку.

Фото 5. Прорезь для клавишного переключателя вырезана из дерева с помощью лобзика. Над переключателем есть место для светодиода. Таким же образом я сделал круглое отверстие для блока предохранителей.
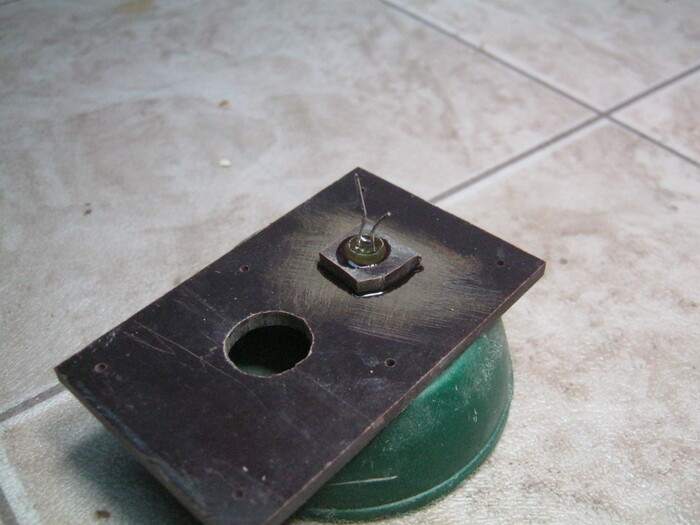
Фото 6. Светодиод, установленный на патроне. Сборка - капля эпоксидной смолы.
Корпус агрегата я собрал с помощью столярного клея ПВА и мелких гвоздей, а в верхних частях просверлил отверстия. После сборки остатки клея сразу удалил влажной тряпкой.
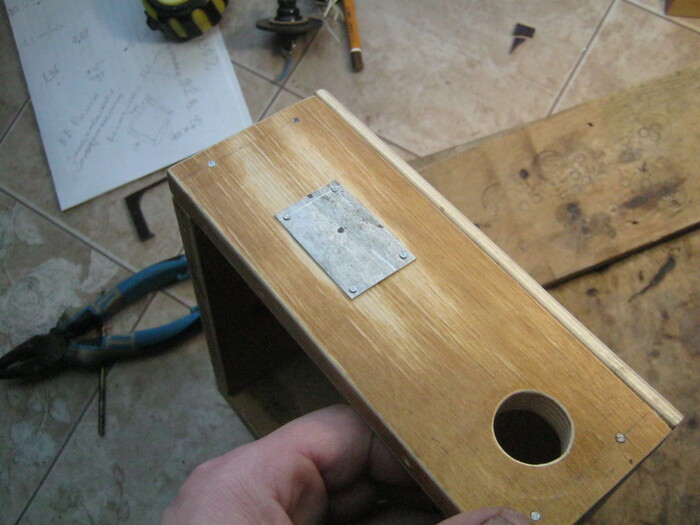
Фото 7. Лишний проем, оставшийся в наследство от трофейных деревяшек, закрыли куском алюминиевого листа. Закрасю.
Обратите внимание: Что нужно учитывать при обзвоне постоянных клиентов.
Остальное - блок предохранителей.Подставка для рабочего инструмента – термопроволока, изготовленная из тонкой медной трубы. На крышке ящика они закреплены в переходных элементах – деревянных опорных площадках. Последний был вырезан из сухой березы.
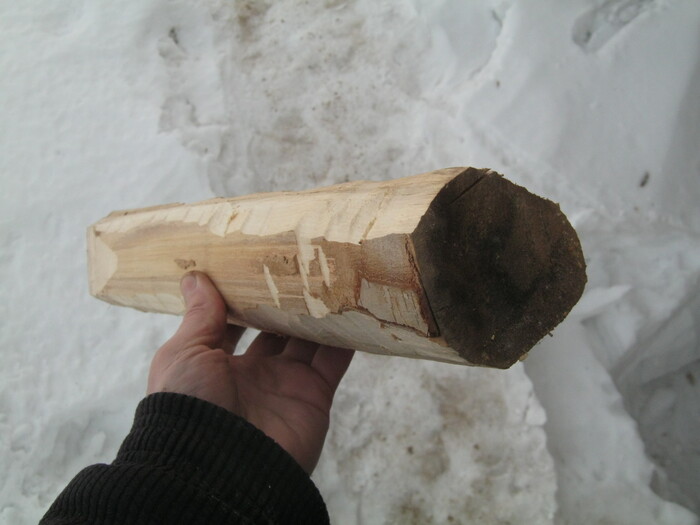
Фото 8. Предмет для токарной обработки – березовое прямослойное бревно без дефектов, разрезанное топором до более или менее круглого сечения.
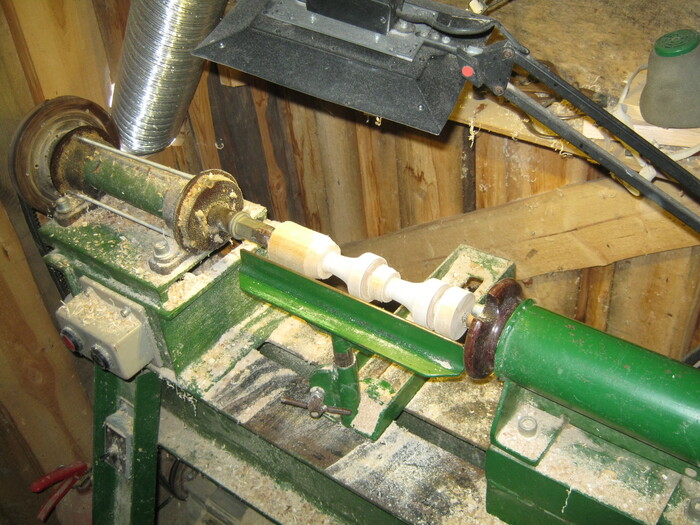
Фото 9. Из одной заготовки вырезаются два простых элемента.
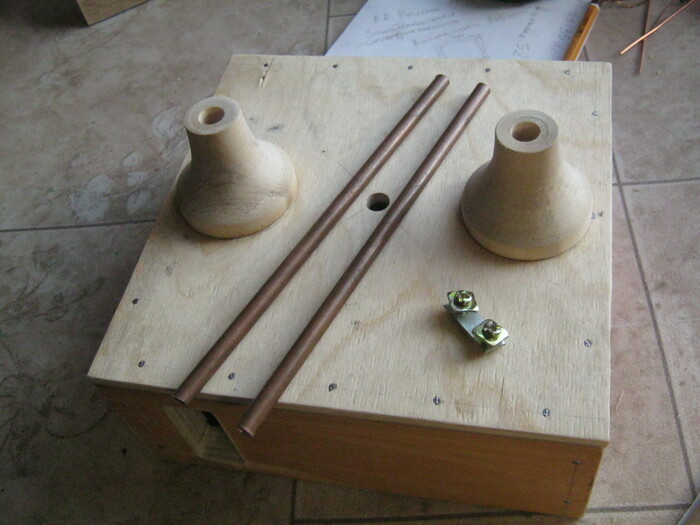
Фото 10. Деревянные опоры крепятся к крышке с помощью деревянного ПВА и гвоздей. Рядом лежат заготовки стойки — куски медных трубок и винтовой разъем от заводского хомута.
Клеммник был расколот ювелирным лобзиком на две равные части и припаян к концам медных трубок. Огненная пайка. Контактный винт со второй пластиной снят и детали очищены. Для пайки пламенем и оловянного припоя использовалась флюсовая паста. После смыва остатков флюса резьбу на разъеме восстановили метчиком.
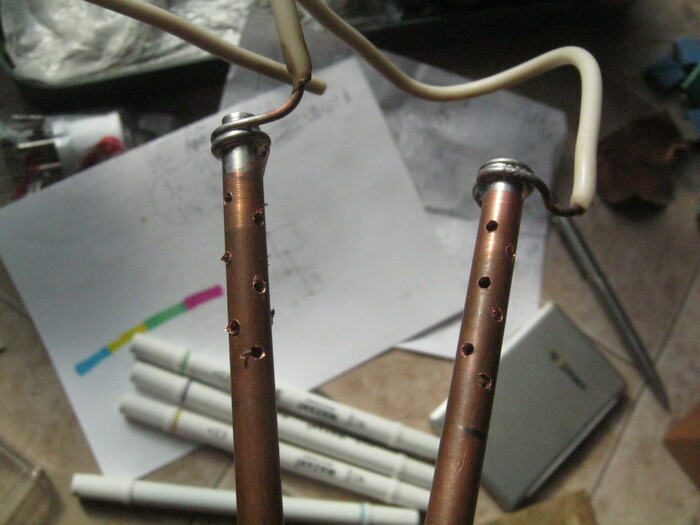
Фото 11. Нижняя часть медной трубы стоит с припаянными проводами. Ряд непотайных отверстий – для лучшего сцепления с цементным составом внутри деревянных опор.
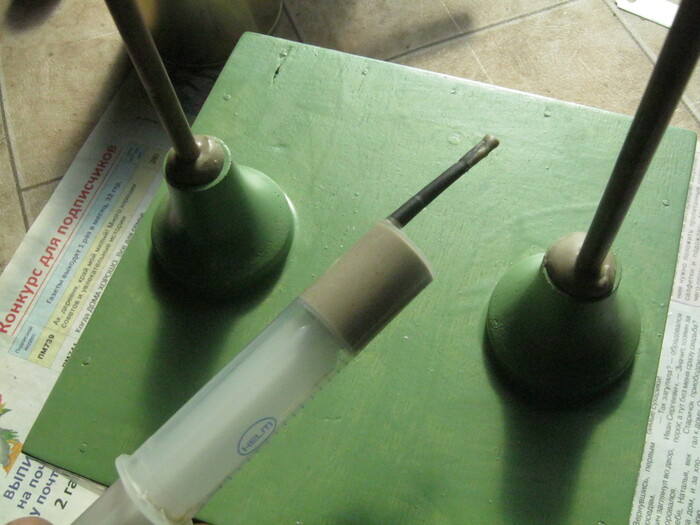
Фото 12. Сборка стеллажа на окрашенном ящике.
Подготовленные трубы заполняются клеящим цементом, изготовленным из жидкого стекла и стеклянной пыли – собранного и высушенного осадка маляра по стеклу. Для глубокого проникновения густого цемента я использовал медицинский шприц с насадкой с удлиненным отрезком подходящей термотрубки. Состав наносили шпателем, сняв поршень шприца.
Сборка и настройка устройства.
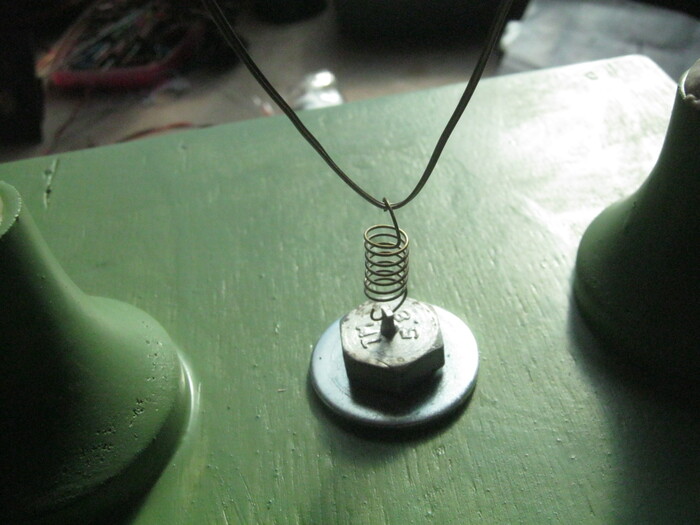
Рисунок 13.
В качестве эксперимента я использовал небольшую пружинку для затягивания нихромовой полупетли; Нашёл как раз подходящее место для крепления — просверлил соосное глухое отверстие под резьбу М3 в головке болта для крепления трансформатора и сделал ушко из куска винта. Это оказалось ерундой. После небольшого прогрева петля прекрасно принимает и сохраняет нужную форму, даже несмотря на то, что изначально она замысловато закручена. На рисунке изображен рабочий элемент из двух нихромовых проволок Ø 0,5 мм.
настройка агрегата подразумевала выбор температуры проволоки – желательно, чтобы ее было больше, но при слишком высокой температуре легкоплавкие стекла начинают прилипать. Это не страшно - при выключении прибора и остывании провода они отделяются через 4...7 секунд из-за сильной разницы ТКР (коэффициента расширения), но работать неудобно. Температуру можно регулировать, меняя обмотки трансформатора, благо их оказалось достаточно; изменить длину и диаметр проволоки. Наконец, плавно и быстро – с внешним LATR.
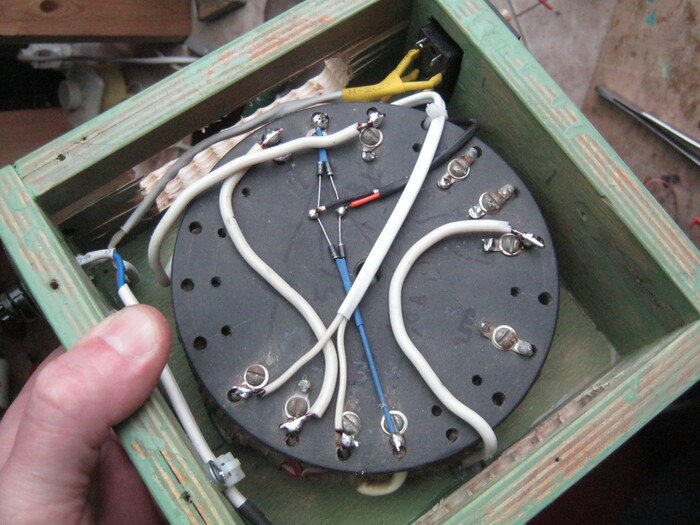
Изображение 14. Вид установки агрегата снизу. Также на боковых стенках ящика можно увидеть забытые отверстия для вентиляции, сделанные в последний момент.
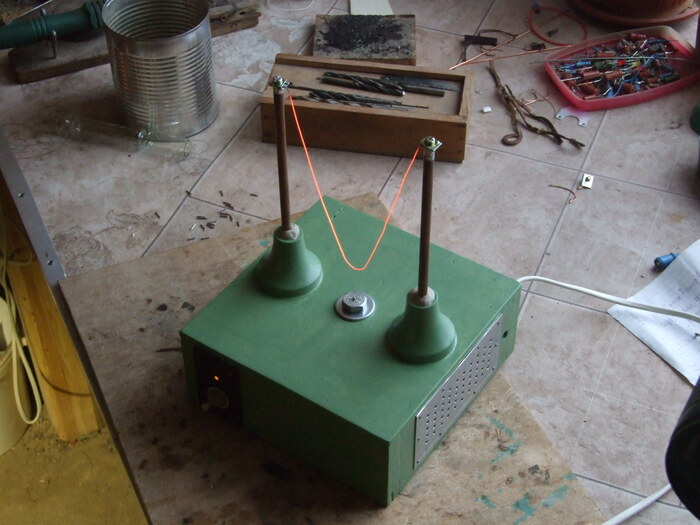
Фото 15. Готовый агрегат в работе. Боковые вентиляционные отверстия закрыты самодельными решетками из тонкого алюминиевого листа.
Как это работает.
В нужном месте стеклянной трубки делают царапину длиной 5...10 мм. Это начало кольцевой трещины. При этой царапине труба прикладывается к раскаленной проволоке. Через полминуты раздается тихое «Крак!». Немного поворачиваем трубу и продолжаем делать трещину до полного соединения концов. Трубка легко ломается.
Следует сказать, что желательно использовать более толстую проволоку; с ним устройство работает гораздо лучше. Классики рекомендуют диаметр 0,7...1,5 мм.
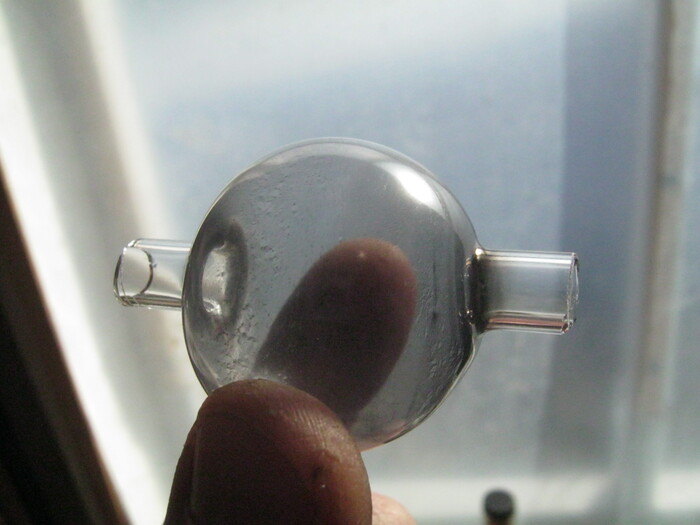
Фото 16. Тренировочный мяч из свинцового стекла (исходный вид - Фото 2). С помощью устройства ноги можно подстричь очень коротко.
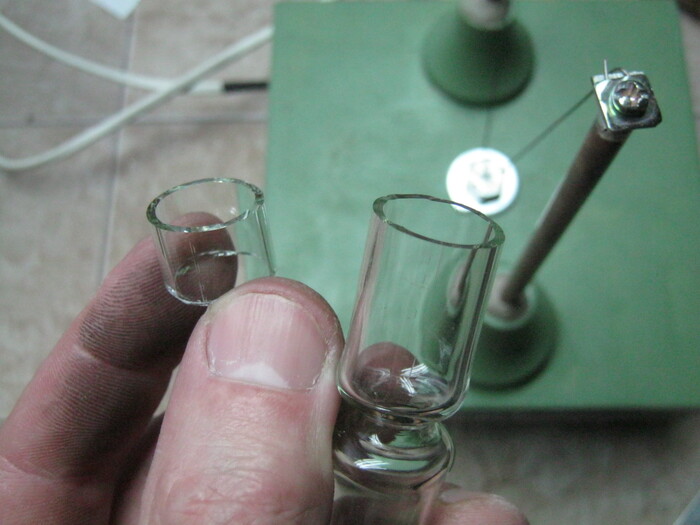
Фото 17. Еще один пример разреза, недостижимого при обычном разрыве, — очень короткий кусок нетонкой трубы.
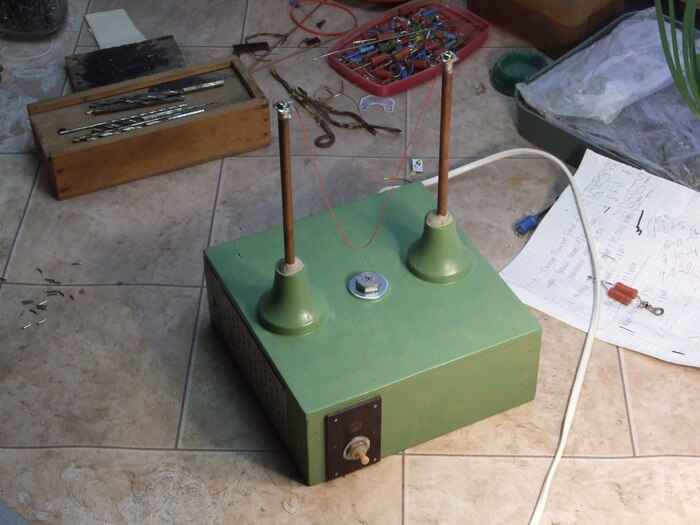
Изображение 18. Внешний вид готового агрегата.
PS Для интересующихся и сочувствующих, у кого есть литература (книги, статьи, заметки) 1920-30-х годов по поводу производства первых радиоламп, поделитесь.
Бабай Мазай, март 2022 г
[моё]Сделай самСтеклоСтеклодувкаХоббиДлинный пост 29 Поддержите ЭмоцииБольше интересных статей здесь: Гаджеты.
Источник статьи: Электрорезка для стеклянных трубок.