
Рисунок 1.
При проектировании небольшого настольного пластинчатого станка для точечной сварки мелких изделий, представляющего собой простое термостойкое соединение тонких пластин и проволок из разных металлов, для внутренней арматуры самодельных электровакуумных агрегатов, как обычно, были допущены некоторые ошибки и просчеты. Представленная работа – их устранение – прошла несколько интересных итераций. Так. Размеры свариваемых деталей невелики, и при проектировании был использован ряд решений для популярного и где-то близкого (никелевая лента) в последнее время вида деятельности - соединения пальчиковых аккумуляторных элементов с аккумуляторами. Такие устройства обычно собираются на основе высоковольтного трансформатора от микроволновой печи, удобного для перемотки. Кроме того, существует ряд доступных и доступных встроенных модулей управления такой сваркой. Все это пошло в дело (Фото 2).
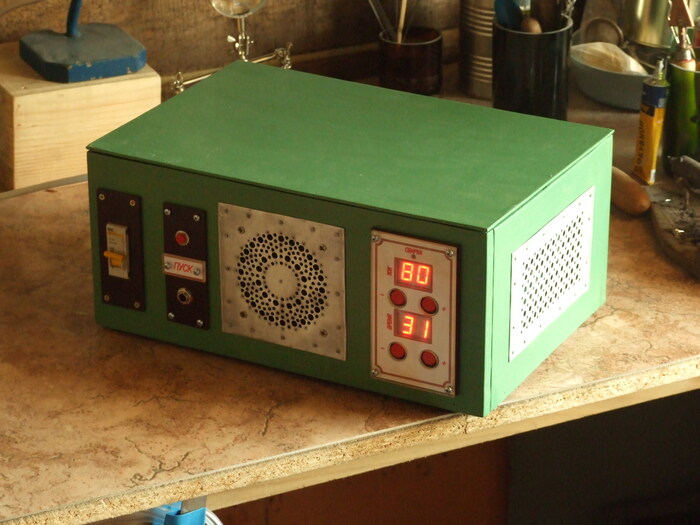
Изображение 2. Первоначальный внешний вид устройства. Его блок питания. С фронта. Клеммы для подключения кабелей к зажимному механизму с электродами сзади.
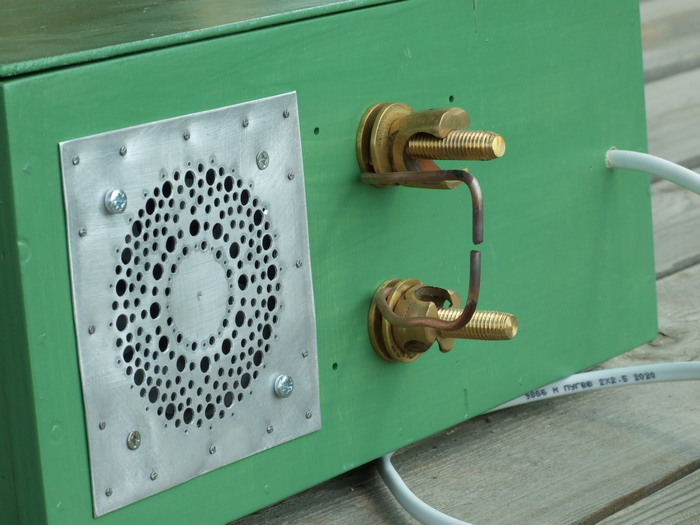
Фото 3. Источник питания для точечной сварки. Задняя сторона.
В выходные клеммы зажимаются простейшие сменные тестовые электроды из медной проволоки диаметром 3 мм. Кстати, это был не самый плохой вариант, хотя и очень неудобный - зазор был маленький, провод сильно нагревался, прилипал к деталям, приходилось оперировать настройками контроллера и запускать его вслепую. Но в целом приготовление было неплохим.
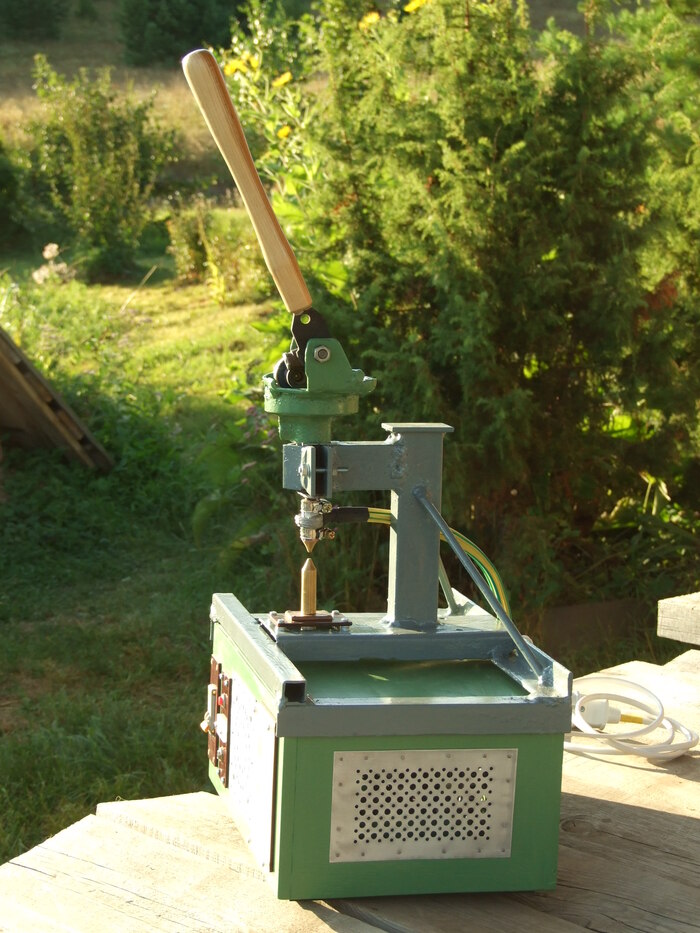
Фото 4. Аппарат точечной сварки, установленный с рычажным механизмом.
Массивные бронзовые электроды, значительное давление, удобно работать. Однако. Сварка была крайне плохой, хуже недоразумений с проволокой (Фото 3) - я недооценил гигантские токи, и сварочная цепь оказалась составной из слишком многих частей. И хотя я старался сделать их массивными и с изрядным сечением, общее падение напряжения оказалось большим и мешало сварке. А в силовой трансформатор было вставлено всего несколько витков кабеля — напряжение на нем изначально было низким.
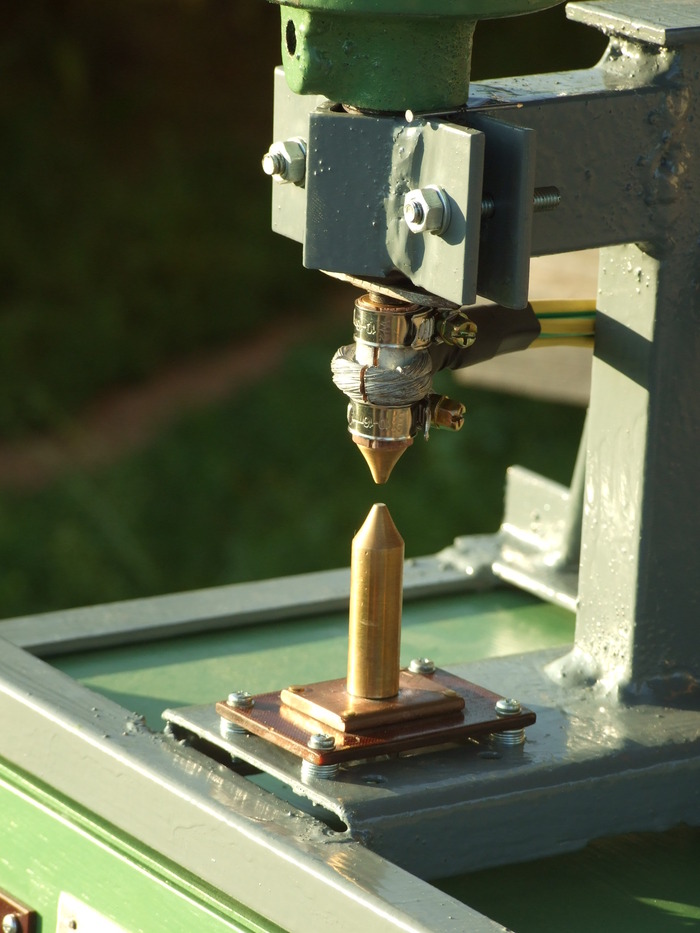
Фото 5. Электроды на сварочном аппарате большего размера.
Поплакая отведенное время - "Ах, где были мои глаза!", я проанализировал конструкцию и способы ее оживления. Их ровно два – преобразовать сварочный трансформатор в аналогичный, но с более высоким напряжением, чтобы можно было пренебречь имеющимися потерями. Устранить, минимизировать сами потери. Первая задача разбивается еще на две – перемотать имеющийся трансформатор или сделать новый, более мощный, если место в корпусе это позволяло. Кстати, можно было бы сделать несколько переключаемых отводов от первичной обмотки и расширить диапазон использования. Планировалось перемотать более тонкую шину, чтобы вместить больше витков.
Перевернув свой механизм, я пришел к неутешительному выводу – воссоздавать его было бы слишком материально и трудозатратно; ряд деталей был изготовлен так, а не иначе из-за ограниченных технических возможностей существующего цеха. Простейший вариант с проволочными электродами и ручным зажимом также внушал осторожный оптимизм (Фото 3).
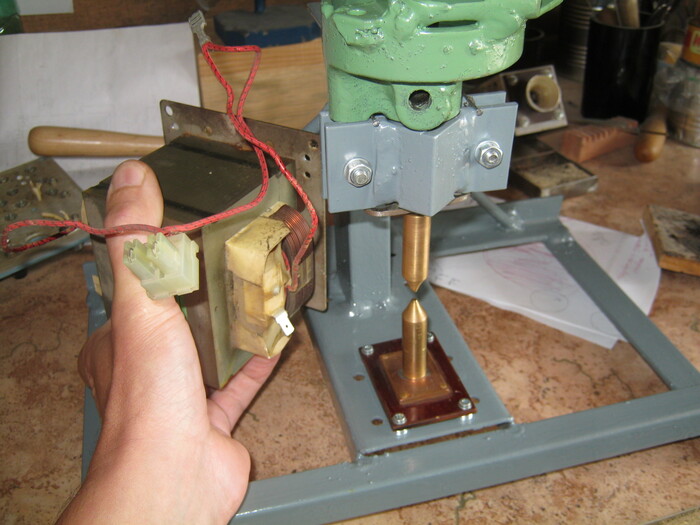
Фото 6. Возможный вариант устранения потерь — трансформатор с длинными мягкими вторичными проводами, расположенными рядом с электродами, сбоку каркаса. Для жестких, нетонких деталей.
Мне очень хотелось использовать хорошо сделанный сварочный трансформатор с запаянными клеммами. В импульсе был собран простой вариант механизма перемещения электродов, встроенный в корпус (Фото 7).
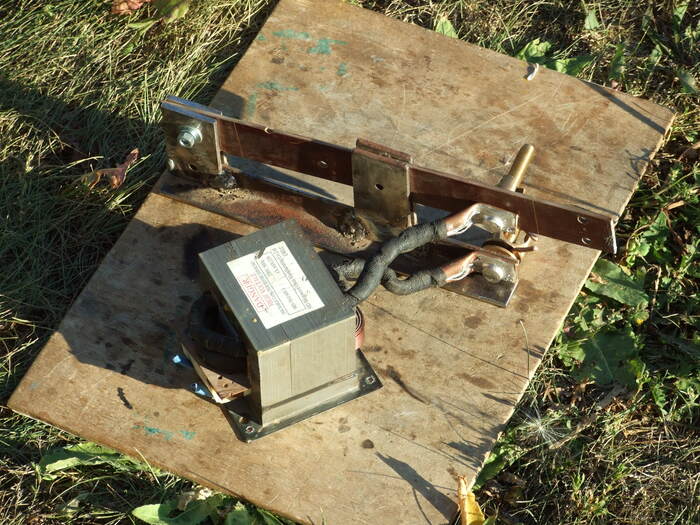
Фото 7. Средний, аварийный вариант компрессионного механизма.
Трансформатор с зажимами - от предыдущей версии. Верхний текстолитовый рычаг можно удлинить деревянной рукояткой для увеличения силы сжатия. Электроды легкозаменяемые, плоские, вырезанные из пластины. Сварилось очень хорошо - потери минимальные, но ход рычажного узла был не очень плавным. Провода от трансформатора короткие и жесткие — при пайке вдоль проводов капиллярные силы втянули припой и превратили их в стержни.
Поразмыслив о проделанной работе, я принял коллективное решение перемотать имеющийся трансформатор на более высокое напряжение на вторичной обмотке и сделать длинные мягкие выводы. Этого удалось добиться, используя в качестве проволоки плоскую самодельную рейку из фольги (Фото 8). Тогда же родилась соответствующая конструкция для прижима электродов — плоские пружинные кронштейны, которые перемещаются только за счет своей гибкости. Как пинцет (Фото 9).
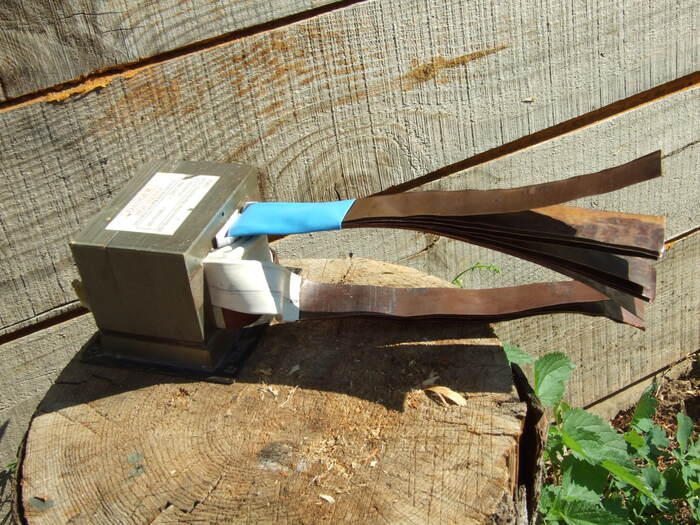
Фото 8. Трансформатор намотан обратно с плоской шиной. При сопоставимом с предыдущим поперечном сечении нам удалось втиснуть еще один виток.
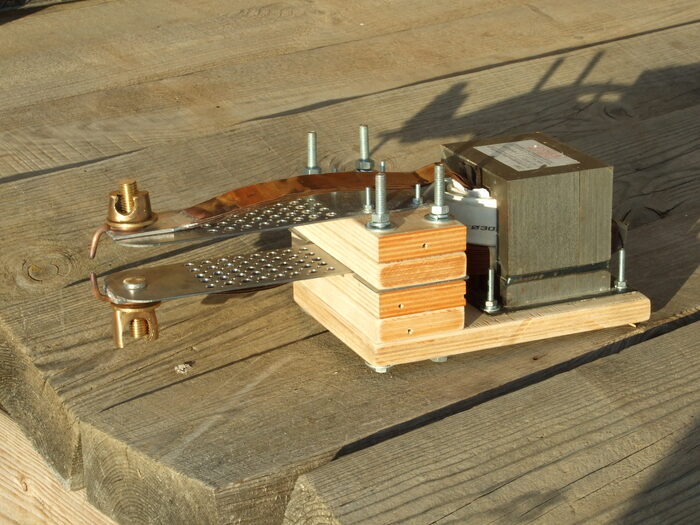
Фото 9. Пинцетная конструкция электродной системы.
Электроды — та же эрзац-проволока, но она тоже хорошо справляется с мелочами. Конструкция сработала на удивление хорошо - сваривается отлично, ход пластин исключительно плавный, давление "вручную" для деталей из проволоки и пластин толщиной до 0,4...0,5 мм вполне хорошее, электроды даже из тонкой меди почти не коли.
Обратите внимание: На днях мне сказали, что профессиональные фотоаппараты больше не нужны, потому что телефоны сейчас снимают также. Так ли это?.
Детали такой толщины свариваются с настройками контроллера на половинной мощности и времени – сварятся и более толстые, но потребуются электроды большего размера. Электроды, в отличие от оригинального стержневого варианта (Фото 5), можно легко сделать выступающими вперед для внутренней сварки. Приговор – принять его с радостью.Доработка устройства.
Что было необходимо для работы.
Набор небольших инструментов для металлообработки, деревообработки и электромонтажа. Крепеж, мелочевка, расходники, лакокрасочные материалы.
К точке.
Пробная сварка двумя последними механизмами проводилась при питании сварочного трансформатора от существующего контроллера, установленного в коробке (Фото 10).
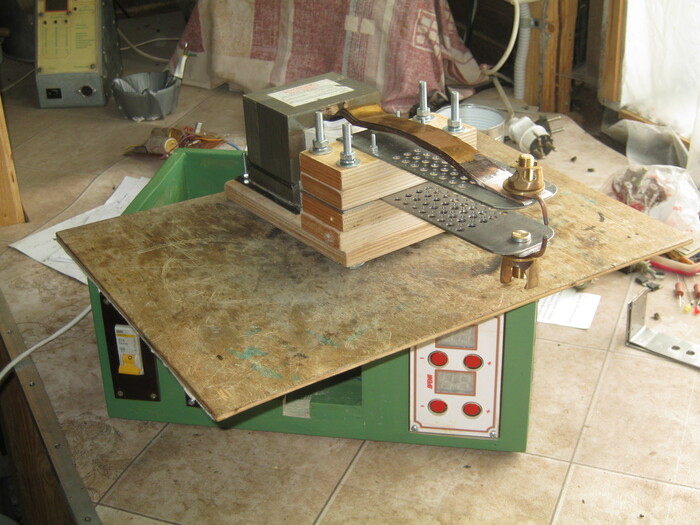
Фото 10. Эксперименты с новым механизмом. Последний крепился к коробке и подключался к штатному контроллеру короткими проводами.
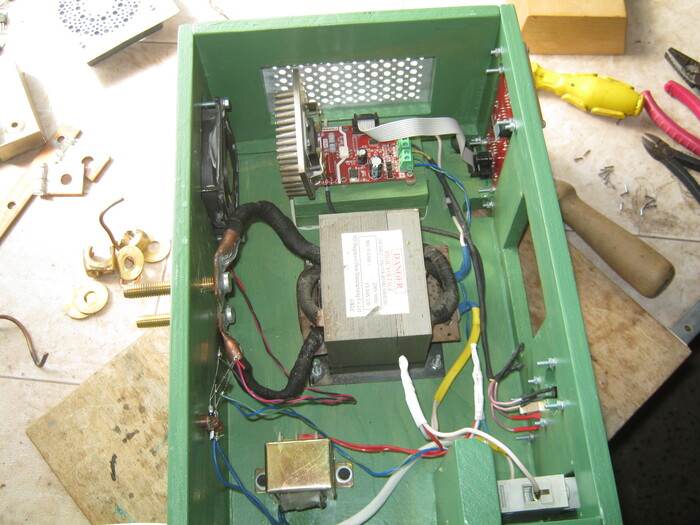
Изображение 11. Конец, начало.
Демонтирован один из вентиляторов с панелью, обдувающей силовой трансформатор. Более чем ожидалось, короткие тупые гвозди, которыми он был прикреплен к деревянной стене, были удалены без особого труда и вандализма. В новой версии все доступные для манипуляций органы устройства будут спереди.
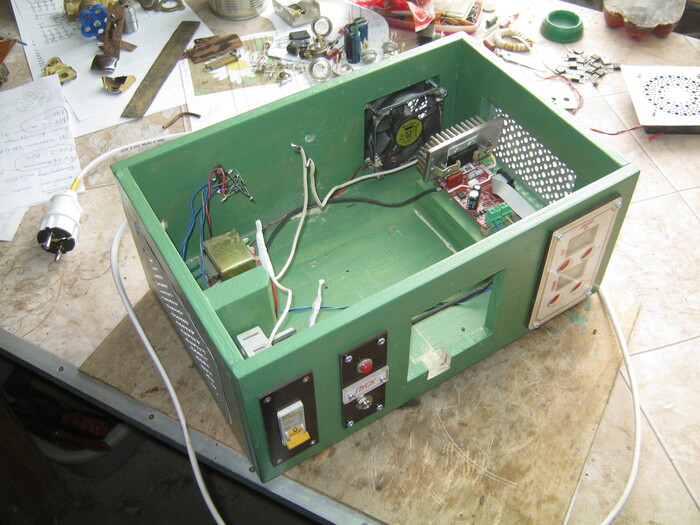
Фото 12. Трансформатор с сильноточными выводами демонтирован. На задней стенке еще есть свободное место, перенесем туда позорный вентилятор. Не помешает, да и обидно за красивое самодельное панно.
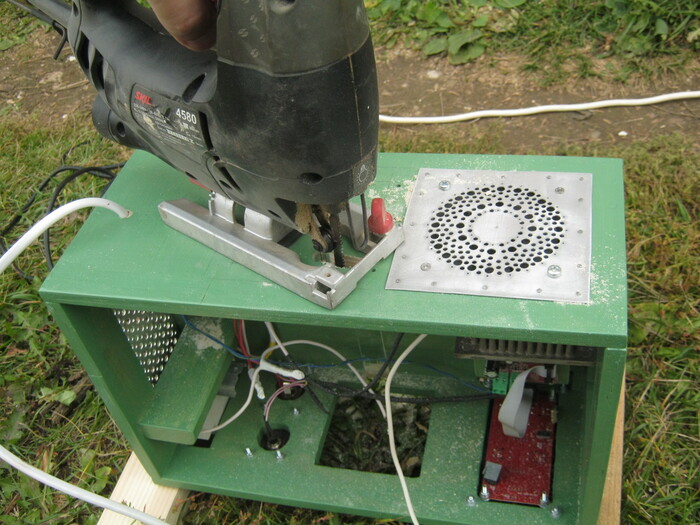
Фото 13. Простым карандашом разметил место отверстия, просверлил входное отверстие для напильника и вырезал электролобзиком.
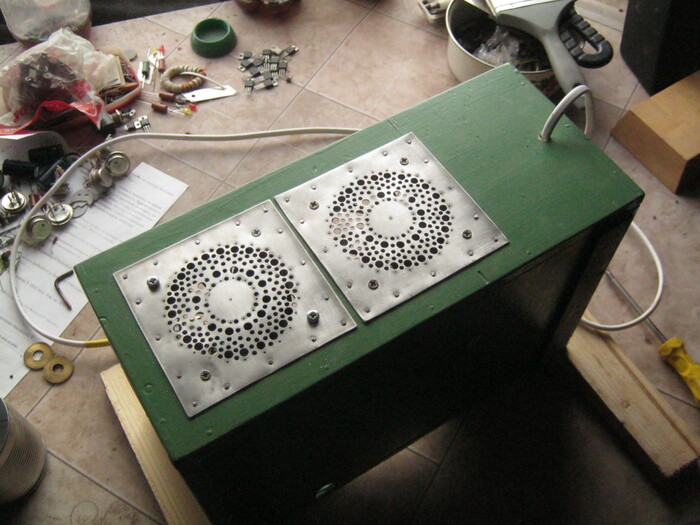
Фото 14. Смонтировали панель с вентилятором, прибили такими же нарезанными маленькими гвоздями. Чтобы слишком толстая фанера стены не вибрировала, я поместил внутрь тяжелую железку.
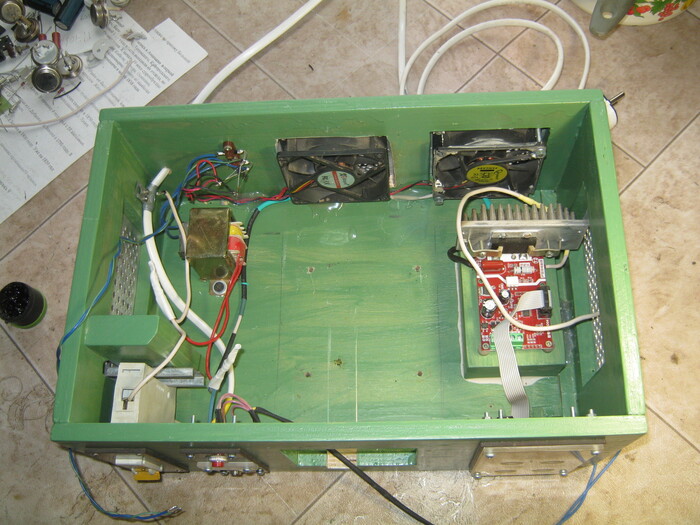
Фото 15. Проложил провод от только что установленного вентилятора к выпрямителю на стене и подключил его параллельно первому.
Зачистил и подготовил место для установки трансформатора с электродами - починил поврежденный при распиловке провод, удлинил несколько проводов, уложил и закрепил их по углу.
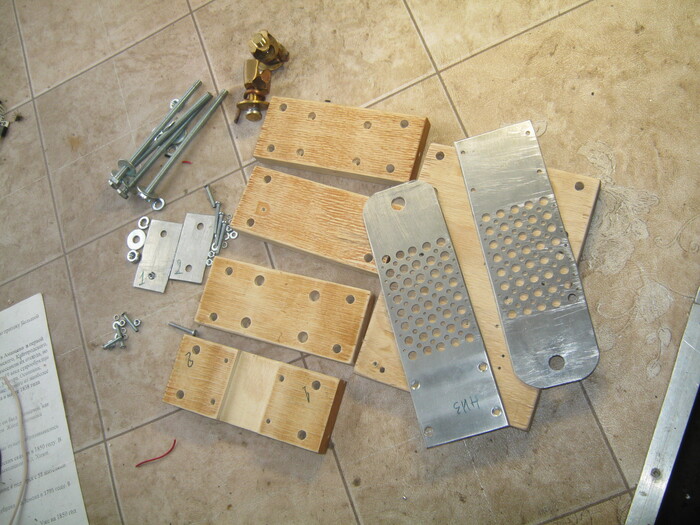
Фото 16. Детали платформы с изолятором и электродной системой. Разобрано до атомов.
Перед сборкой я несколько раз покрыл деревянные детали акриловым лаком. Меня соблазнило быстрое высыхание. Конечно, благополучие. Чтобы надежно сохранить древесину, следует использовать масляный лак или краску.
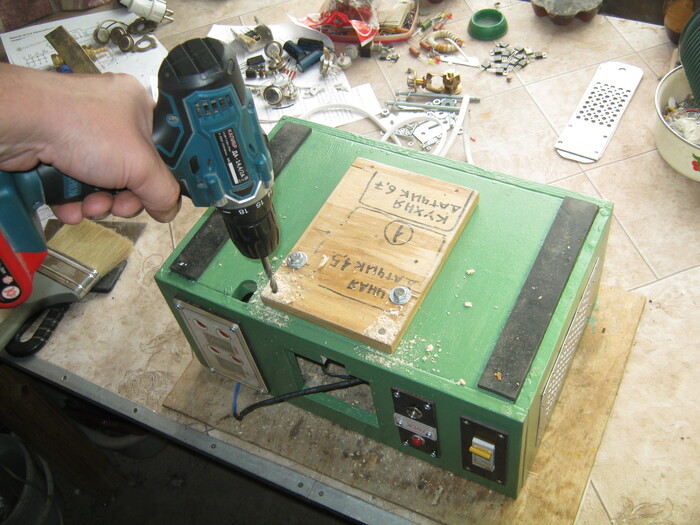
Фото 17. Модуль с трансформатором и электродами довольно массивный. К счастью, с надежным креплением к корпусу проблем не возникло – естественно части модуля – сборная изолирующая подставка и трансформатор крепятся длинными сквозными винтами.
Всего восемь штук. Их длина несколько чрезмерна, и достаточно собрать этот модуль сразу внутри корпуса с креплением через него, в том числе через днище, и проблема решена. На фото показаны отверстия, которые просверлены в нижней части коробки. В качестве проводника используется основание электродно-трансформаторного модуля.
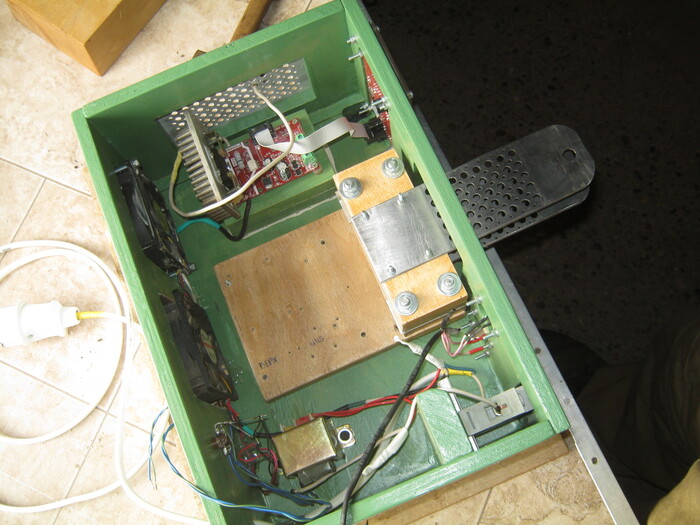
Фото 18. Электродная система собрана в коробке. Послойно, внизу крепятся обычные болты М6.
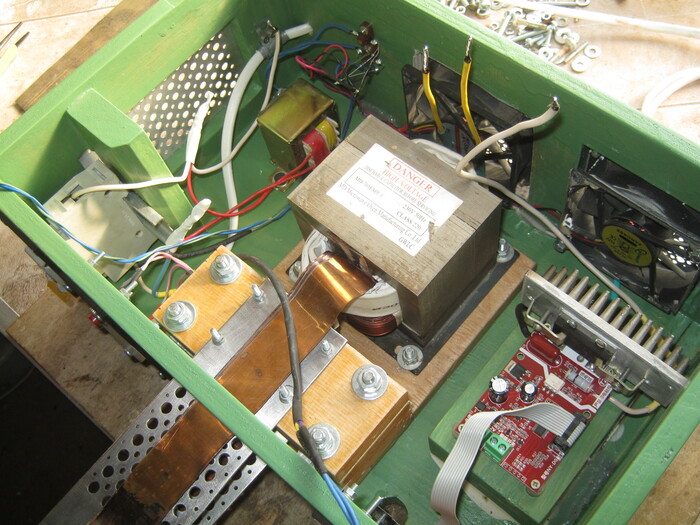
Фото 19. К выводам трансформатора предварительно была припаяна пара коротких, сверхпрочных проводов и изолирована термотрубкой. Для удобства подключения. Я обошел плоские клеммы на шине и прикрутил трансформатор винтами М5. Тоже насквозь, через дно материи.
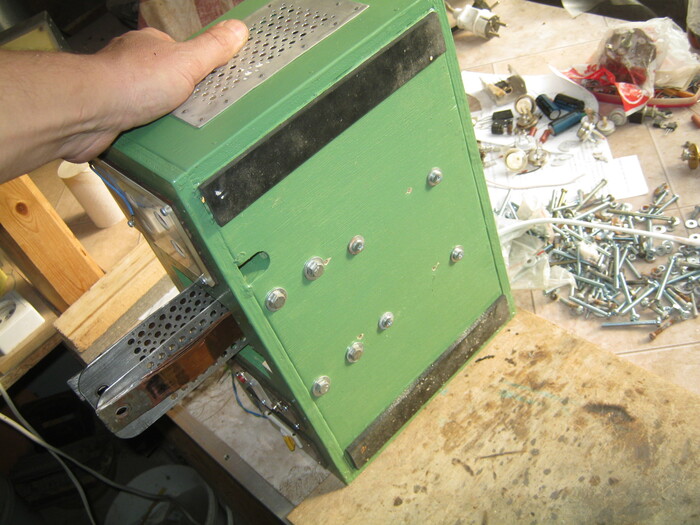
Рисунок 20. Вид на нижнюю часть коробки. Под головки винтов я подложил широкие армированные шайбы. Ножки корпуса изготовлены из полосок плотной 5-миллиметровой резины, что позволило использовать неутопленные крепления.
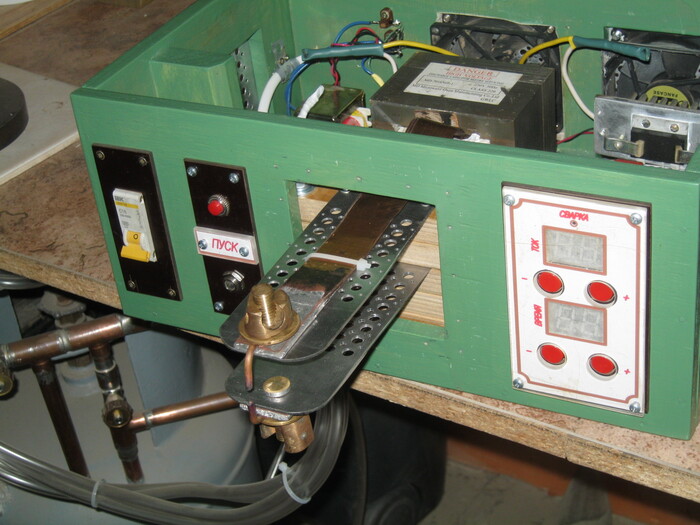
Рисунок 21. Вид передней стенки установки в сборе с новым электродным модулем. Установил винтовые клеммы, зажал электроды, восстановил электропроводку внутри коробки и проверил работоспособность. Компактный, мощный, отлично работает - о да Пушкин!
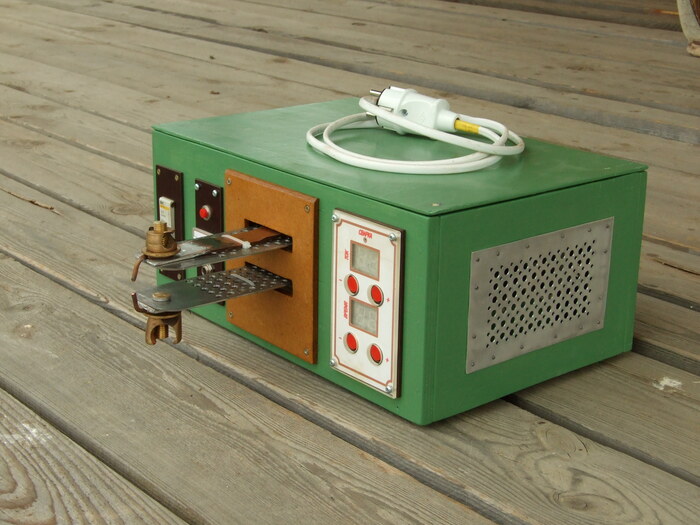
Фото 22. Некрасивое отверстие вокруг электродов закрыли декоративной фанерной крышкой.
Из тонкого листа твердого ДВП я вырезал заготовку, разметил ее, лобзиком вырезал прорези для электродов и просверлил отверстия для крепежа. Отшлифовал и покрыл пару слоев масляного лака.
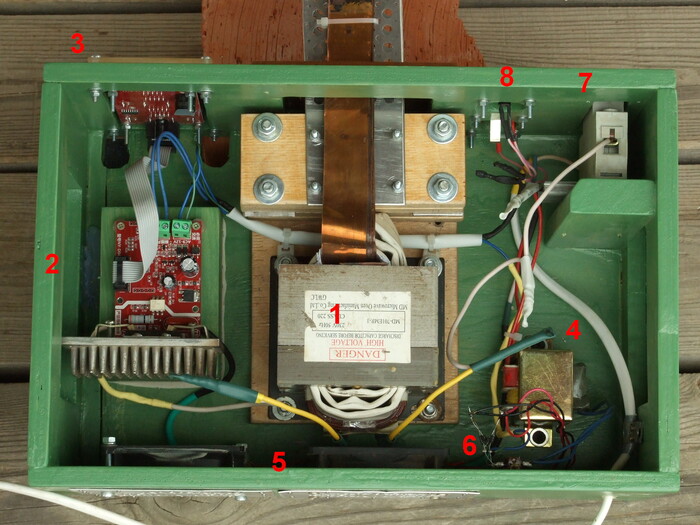
Рисунок 23. Вид установки устройства.
Где: 1 – сварочный трансформатор; 2 – модуль управления; 3 – субмодуль управления с индикацией, кнопками и звуковым сигналом; 4 - сервисный маломощный трансформатор для питания модуля управления и вентиляторов охлаждения; 5 – вентиляторы охлаждения, работающие на половинной мощности; 6 – выпрямитель управления вентиляторами – диодный мост; при необходимости увеличить расход воздуха, добавив оксидный конденсатор; 7 – автоматический переключатель; 8 – кнопка запуска и гнездо для подключения педали.
Версия аппарата окончательная, возможные модернизации заключаются только в использовании более совершенных электродов, например, каплевидных из нетонкого листа и использовании внешнего сварочного пинцета.
Настольный аппарат контактной сварки для электровакуумных работ. Автореферат.
Бабай Мазай, сентябрь 2022 г
[my]Технологические поделкиСделай самЭлектроникаЭлектроконтактная сваркаТочечная сваркаХоббиСамодельные инструментыСваркаLong Post 5 Support FeelingsБольше интересных статей здесь: Гаджеты.
Источник статьи: Аппарат небольшой мощности для контактной сварки «насквозь».